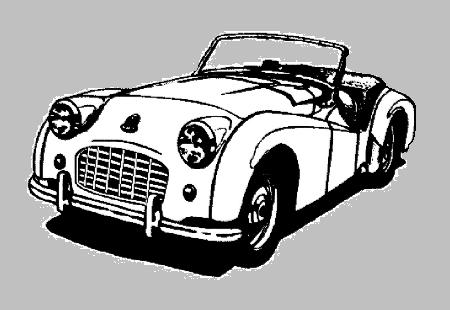
TR2-4 Rear Differential Overhaul
Macy's Garage, Ltd.
America's BEST
Triumph Shop! |
Tools and tips for overhauling Triumph TR2-4 rear
differentials
Let me begin by saying that I do not intend to re-write the
factory workshop manual with regard to rear end service. This is a
supplemental article to demonstrate a) what a huge job this is , and b) how I
came up with substitutes for all of the special tools demonstrated in the
Standard-Triumph Service Instruction Manual (TR2-3) or Workshop Manual
(TR4-4A). This also will not address rear axle bearing and seal
replacement, which can be performed without overhauling a differential.
As always throughout my site, click on the
thumbnail photos for a larger view. Use your browser's BACK button to
return.
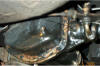 |
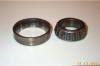 |
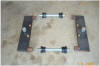 |
Understand that you will not be performing
rear end service with the unit in the car. The spare tire well is too
close to remove the internal parts. Arrow points to a recess used to
apply pressure to the case and spread it open (later). Most folks
performing a full frame up restoration will only sandblast and paint the
rear axle. This is a shortcut you really shouldn't take. |
And here's why you want to overhaul your rear
differential, especially if the car has sat idle for a number of years.
Pitting on this carrier bearing and race was caused by rust. On a car
which has sat idle for years, oil drains off of the internal parts, and
moisture from humidity finds its way in through the breather opening causing
unseen damage. |
The first tool you'll need is a casing
spreader, Churchill S101. You'll never be able to find one! I made mine
from 3/8" bar stock, 1" pipe, and 3/4" fine threaded rod. The
small bolts are grade 8, and close to the edge of the bar stock, so 1/2"
bolts were tapped into the bar stock at the location of the depressions
shown in photo #1 to help push. Jam nuts are used on the 1/2" bolts to
lock in place. |
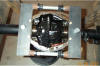 |
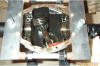 |
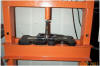 |
Here's the spreader in place on the rear
housing. Use the longest wrenches you have, as this will require a
terrific amount of force to obtain the few thousandths needed to extract the
differential from the housing. You will also need to apply and release
the pressure several times throughout the overhaul process. |
With the differential unit removed, the
pinion can be driven out as shown in the factory manual. They
recommend a hide faced hammer, but any soft copper or brass hammer
will work just as well. Reinstall the nut (upside down) after removing
the flange just to be sure you don't damage the threads. |
The next Churchill tool shown in the manual
is TS1 and S4221 to remove the head bearing from the pinion gear. I
opted to do this in my press with a bearing separator placed below the
bearing. You will need a hydraulic press such as this many times
during a rear end overhaul to remove and install bearings and races. |
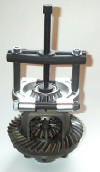 |
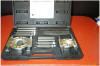 |
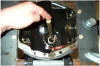 |
Carrier bearings are removed with Churchill
tools S103 and S4221, but a universal bearing separator and puller will do
the same job. I purchased an optional stepped washer to fit in the end
of the carrier which gives the puller something to push against. This
unit will not fit in the large press for bearing removal. |
Here's the complete Bearing Separator Push -
Puller set. This is an OTC 4518. You'll want a good set, as many
of the bearings have to be removed and installed several times as you check
for clearances without shims, then remove bearings and races to add shims,
then re-assemble to check for proper clearances until you get it right. |
Pinion bearing races are driven out with
Churchill tool 20SM and FT71, or use a brass drift and big hammer.
Just FYI, for the larger pinion head bearing race you will be driving
against shims, all of which will be destroyed and need to be replaced. |
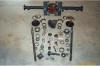 |
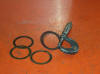 |
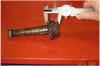 |
Here's what you get when everything is apart.
While you're in here, I recommend wholesale replacement of all bearings and
races. You wouldn't want to have to go back and ever do this job
again! Rear axles are shown apart as part of a complete overhaul, but
are not addressed in this article. |
A good micrometer will be necessary for
reassembly to verify shim thickness, both old and new. You should be
proficient at using it too! |
Dial calipers are also mandatory for
overhauling a rear end. Here we measure the pinion head thickness
because Triumph set the pinion depth from the bottom of the pinion with a
special tool, and we'll have to measure from the top of the pinion with
modern tools. Math to 4 decimal places will be required! |
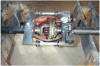 |
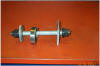 |
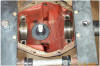 |
A dial indicator and magnetic base is another
must have for this job. You'll need it to measure the carrier run out,
casing end float, crown wheel and pinion backlash, and for checking and
adjusting the axle end float on both sides. |
The workshop manuals show that Churchill tool
M70 was needed to install the pinion head and tail bearing races, so I made
something similar out of some remaining 3/4 threaded rod from the case
spreader. |
While my home made tool did work, it was a
struggle. Especially for the head bearing race, which is always a very
tight fit. This race is another one that is in and out several times
during the process to fit the shims which control the pinion depth. |
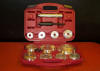 |
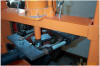 |
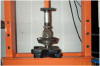 |
A nice bearing race and seal driver set like
this Lisle 12800 is a great tool, especially for installing axle seals in
the rear end housing, but it was no match for the pinion head bearing race. |
In the end, I found that the 20 ton press and
the proper assortment of washers, pipe nipples, and steel bars resulted in
the easiest way to install this difficult bearing race back into the rear end
housing. |
Tool S103 and press S4221A are
recommended to fit the head bearing on the pinion, and in a similar
operation tools S100 and handle #550 are specified to install the carrier
bearings to the differential. With the right diameter and length of
pipe to push the inner bearing races, both can be installed in the hydraulic
press. |
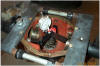 |
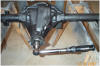 |
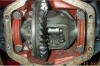 |
The factory utilized a dummy pinion and gauge
(M84) to check the pinion depth, and that's another tool you'll probably
never ever find. Here is my Powerhouse Products POW356000 pinion depth
setting tool in action. This is done by a completely different method than
what's shown in the manuals, so if you're going to buy this tool, buy the
video that goes with it too or you'll never figure it out! The video
is POW902070. |
Once again, special tool 20.SM.98 is
recommended to check the pinion bearing pre-load. This can be easily
accomplished with a torque wrench calibrated in inch-pounds. You'll
get plenty of practice with this, as the pinion will be in and out of the
housing several times until you find the right combination of shims to get
the pre-load within the correct range. |
Here's the completed differential, all nice
and clean inside with fresh bearings, seals, and correct clearances.
Start to finish, this is a 10-12 hour job when all of the right tools or
acceptable substitutes are on hand. Without the tools, there's no
possible way that you'll be able to accomplish this job and build a rear end
that will last for very many miles. To purchase and make all of the
tools shown here is a sizeable investment, so if you only plan on doing one
rear end it will be far more economical to ship your rear differential here
to Macy's Garage or find someone locally who has plenty of experience with
Triumph rear ends (and the tools). |